Self-tapping screws, also known as metal screws, sheet metal screws, tapping screws, or tapper screws, are versatile fasteners widely used in various applications. Their unique design allows them to create threads as they are driven into a pre-drilled hole, eliminating the need for nuts or additional threaded inserts. In this article, we will delve into the world of self-tapping screws, exploring their types, applications, and essential considerations for a successful installation.
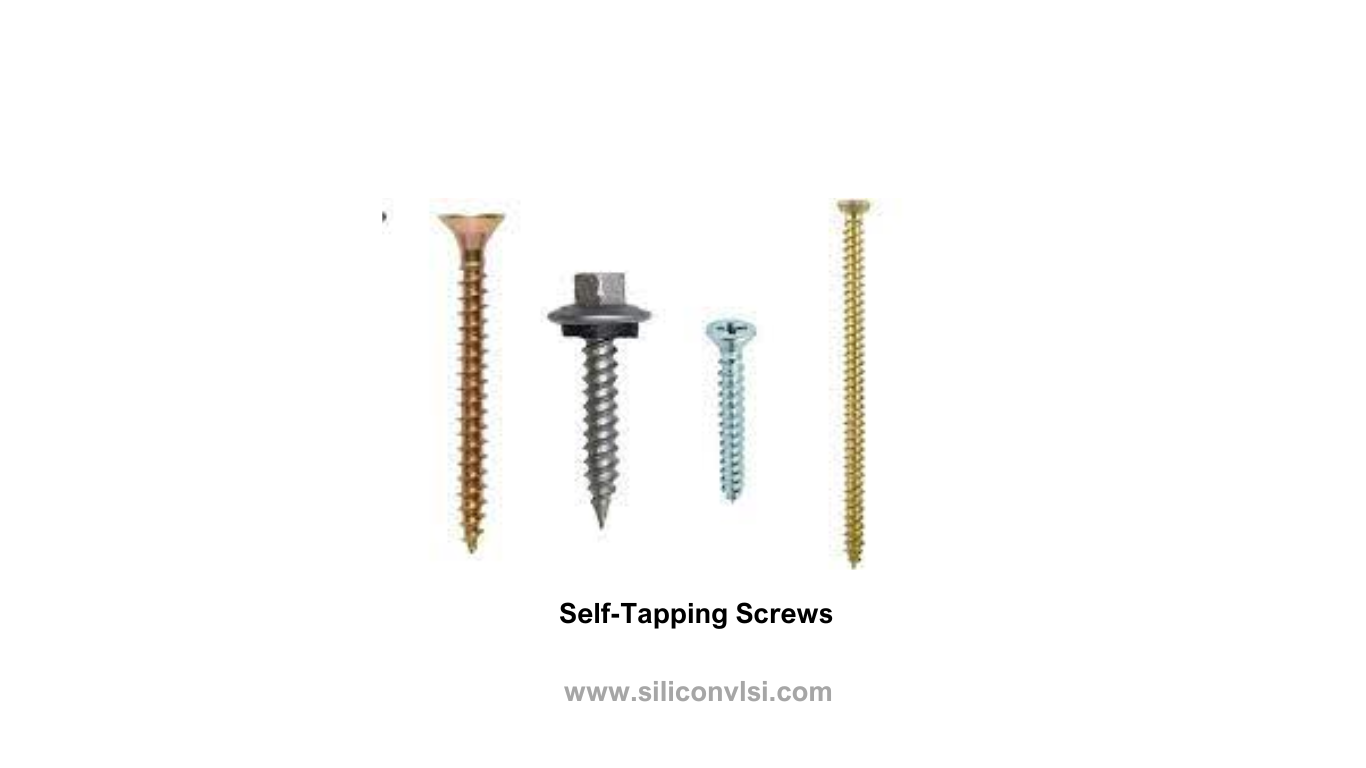
Types of Self-Tapping Screws
Thread-Forming vs. Thread-Cutting vs. Thread Rolling Screws
Self-tapping screws come with different tip shapes and thread formation methods. The tip of the screw can be pointed, blunt, or flat, each serving a specific purpose. Pointed screws are thread-cutting, meaning they tap and create threads as they are driven into a pre-drilled hole. On the other hand, flat-tipped screws are thread-rolling, rolling or extruding threads and creating zero clearance between the screw and the material. Blunt-tipped screws are designed for use with softer materials like wood or plastic, where they can form threads without the need for cutting or rolling.
Material-Specific Self-Tapping Screws
Selecting the right self-tapping screw involves considering the material it will be used on. Different types of self-tapping screws are designed for specific materials, including wood, metal, and plastic. Each variant has unique characteristics that ensure optimal performance and secure fastening. It is crucial to match the screw material and design with the material being fastened to maximize efficiency and durability.
Size, Length, and Torque Considerations
The size and length of the self-tapping screw are important factors to consider. The correct size ensures a proper fit and prevents damage to the material being fastened. Additionally, the desired level of torque, or tightening force, required for the application should be taken into account. Proper torque prevents under or over-tightening, ensuring a secure fastening without compromising the integrity of the screw or the material.
Installation and Best Practices
Ease of Installation and Tools
Self-tapping screws are generally easy to install and compatible with various tools, including power drills and screwdrivers. Their self-tapping design simplifies the fastening process by eliminating the need for additional tools or accessories. This versatility makes them suitable for both professional tradespeople and DIY enthusiasts alike.
Avoiding Over-Tightening and Striping Threads
While self-tapping screws offer convenience, caution should be exercised during installation to prevent over-tightening. Over-tightening can strip the threads, compromising the holding power and integrity of the screw. By applying the appropriate level of torque, the fastener can securely hold the material without causing damage.
Importance of Pilot Holes
To ensure proper thread formation and holding power, it is crucial to use pilot holes when installing self-tapping screws. Pilot holes are pre-drilled or pre-punched holes that guide the screw into the material. They help prevent material splitting, facilitate thread formation, and ensure accurate alignment during installation. It is essential to use the correct size and shape of the pilot hole to guarantee optimal performance and durability.
Differentiating Self-Tapping and Self-Drilling Screws
It is important to note that self-tapping screws require a pilot hole when used on metal surfaces, as they cannot penetrate metal without pre-drilling or pre-punching. In contrast, self-drilling screws possess drill bit-like tips that can create their own pilot holes as they are driven into the material. This key distinction makes self-drilling screws more suitable for metal applications where a pilot hole may be impractical or time-consuming.