Introduction to RTO DRC Rule
The Retapped Out (RTO) Design Rule Check (DRC) is an essential component of the design verification process in Very-Large-Scale Integration (VLSI). In the increasingly complex landscape of semiconductor manufacturing, ensuring that designs conform to specific rules is critical for minimizing errors and achieving high fabrication yields. The RTO rule specifically pertains to addressing the integrity of connections within a circuit and ensuring that retapped nodes do not adversely affect the performance of the designed system. This requirement arises from the need to provide robust verification mechanisms that can deal with intricate design considerations.
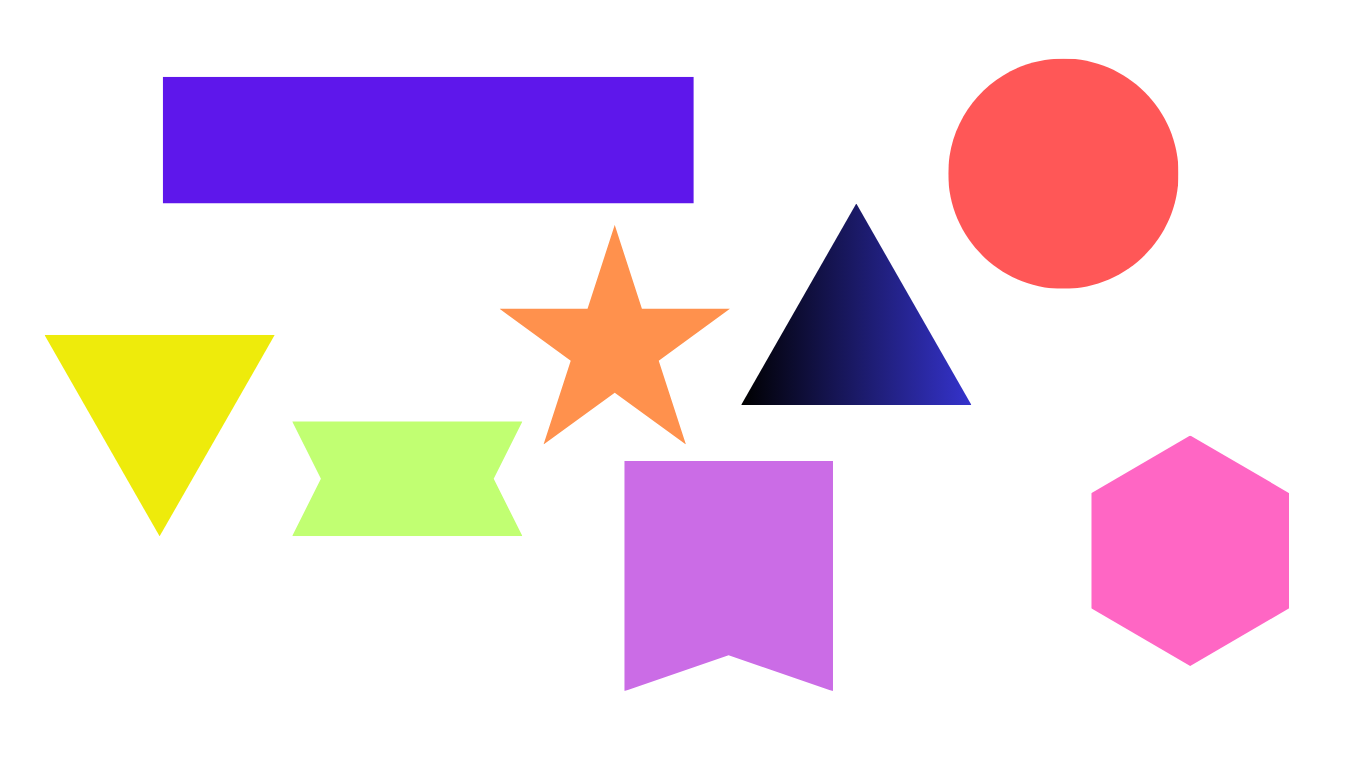
Traditionally, DRCs serve as a set of guidelines to verify that a design meets the necessary constraints set forth by the technology used in semiconductor fabrication. These constraints often include dimensions, spacing, and layering requirements aimed at preventing potential defects during manufacturing. As VLSI technology has advanced, the complexity of circuit designs has increased, necessitating the evolution of DRC rules, including the establishment of the RTO concept. The inclusion of RTO in DRC is critical because it specifically identifies issues related to signals that are retapped, ensuring that they do not introduce parasitic capacitance or other unwanted effects that could compromise circuit functionality.
An important aspect of the RTO rule is its role in enhancing overall reliability and performance in various applications, including digital and analog circuits. The integration of RTO checks into the design verification workflow enables engineers to identify potential problems early in the design process, allowing for timely modifications that can save both time and resources. By understanding the significance of the RTO DRC rule, designers can ensure greater compliance with manufacturing specifications and contribute to the continuous advancement of VLSI technology.
The Need for RTO in VLSI Design
The advent of modern VLSI (Very Large Scale Integration) technology has ushered in an era of unprecedented complexity in integrated circuit design. As industry demands evolve, circuits have become increasingly dense, leading to intricate design frameworks that can present profound challenges. Within this context, the Retapped Out (RTO) DRC (Design Rule Check) rule emerges as a pivotal component, addressing various critical requirements in VLSI engineering.
One significant challenge in VLSI design is maintaining signal integrity, especially as layer counts and interconnects proliferate. The RTO DRC rule aids designers in mitigating risks associated with crosstalk, delay, and signal degradation by enforcing systematic checks that enhance reliability. Furthermore, adhering to this rule can help avert timing issues that arise from reduced signal margins typical in densely packed chips. As clock frequencies increase and operational speeds soar, the importance of timing analysis becomes paramount.
Design reliability is another essential aspect that necessitates the implementation of the RTO rule. Without it, designers often encounter various pitfalls, such as inadequate spacing between critical components or insufficient power supply routing, leading to potential failures post-manufacturing. Such oversights can result in costly redesigns and significant time delays. By incorporating stringent checks provided by the RTO DRC rule, design teams can ensure adherence to best practices, reducing the likelihood of critical failures and enhancing overall circuit performance.
In summary, employing the RTO DRC rule stands as a necessity in VLSI design. As integrated circuits grow more complex, the challenges related to signaling, timing, and overall reliability intensify. The rule acts as a safeguard against the common pitfalls of modern circuit fabrication, ensuring that designers can efficiently create robust, high-performance chips that meet industry specifications and customer expectations.
Impact of RTO DRC Rule on Design Efficiency and Quality
The RTO (Retapped Out) DRC (Design Rule Check) rule plays a pivotal role in enhancing design efficiency and overall quality within the field of VLSI (Very Large Scale Integration). By enforcing stringent design requirements, the RTO DRC rule serves as an early detection mechanism that identifies potential design flaws during the initial stages of the design cycle. This proactive approach allows designers to address discrepancies before moving on to more advanced phases, effectively mitigating the risk of costly revisions once production has commenced.
One of the key advantages of implementing the RTO DRC rule is the significant reduction in time and expense associated with design modifications. By uncovering issues such as layout violations or suboptimal configurations, engineers can make informed decisions and execute targeted corrections without the pressures typically associated with post-production alterations. Consequently, this careful scrutiny leads to a more streamlined design process and promotes operational efficiency.
Moreover, as products evolve within an increasingly competitive market, quality assurance becomes imperative. The RTO DRC rule not only cultivates better design practices but also fortifies product durability, ensuring that devices function as intended under varying conditions. In summary, the integration of the RTO DRC rule in VLSI design processes serves as a cornerstone for enhancing both efficiency and quality, demonstrating its indispensable value within the industry.
Why RTO DRC Rules are Important?
- Avoid Rework: Catching errors in DRC helps avoid the need for RTO.
- Reduce Costs: RTO requires re-generating photomasks and re-fabrication, which is extremely expensive.
- Improve Yield: Ensuring DRC compliance increases the chance of first-time-right silicon, reducing yield loss.
Common DRC Rules to Avoid RTO
- Minimum Metal Width and Spacing: Ensures that the width of interconnects and the spacing between them are sufficient to prevent short circuits and electromigration issues.
- Enclosure and Overlap Rules: Ensures proper enclosure of contacts and vias by metal layers.
- Antenna Rules: Ensures that long metal wires don’t accumulate excessive charges during fabrication, which could damage the transistors.
- Minimum Area Rules: Ensures that certain layers have sufficient area to avoid manufacturing issues.
- Edge and Overlap Rules: Checks that edges of metal and other layers are aligned and properly enclosed.
The RTO (Retapped Out) DRC rules ensure that any issues are caught before the design is sent for fabrication. The purpose of these rules is to prevent costly rework. Common DRC rules include checks for metal spacing, line width, enclosure, antenna effects, and minimum area. Adhering to these rules minimizes the risk of an RTO, saving time, cost, and resources in semiconductor manufacturing.
Future Trends and Advancements Related to RTO DRC Rules
The landscape of VLSI design is continuously evolving, with future trends poised to reshape the implementation and flexibility of the RTO DRC rules. One of the most significant advancements is the integration of artificial intelligence (AI) and machine learning in circuit design. These technologies can analyze vast datasets, leading to more efficient design processes and optimization of design rule checks (DRC). By leveraging AI algorithms, design engineers can automate the identification of potential violations based on the RTO rules, thus significantly reducing the time spent on manual checks. This not only enhances productivity but also allows for more complex designs to be evaluated rapidly.
1 Comment
Thanks I have recently been looking for info about this subject for a while and yours is the greatest I have discovered so far However what in regards to the bottom line Are you certain in regards to the supply